8 Ways To Reduce Energy Consumption Of Glass Furnaces
Date:2016-07-01 18:03 From:Zhengzhou Sunrise Refractory Author:sunrise
The energy consumption accounts for 75% of the total energy consumption of glass furnaces. Recently, many measures have been taken to reduce energy consumption.
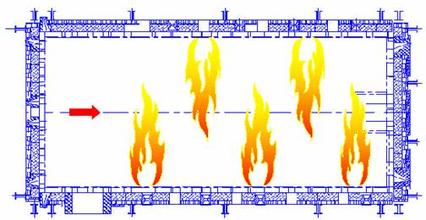
The following 8 ways are turned out to be effective to reduce energy consumption.
(1) One way is to improve the temperature of glass liquid without improving the temparature of flame. This way can speed up the melting of glass, shorten the melting time, improve the production capacity and reduce the energy consumption. Since glass liquid selectively absorbs radiation, the temperature of glass liquid can be improved by increasing the radiation from flame space to glass liquid without improving the temperature of flame. Waves less than 3μm can pass down through the liquid level. Those waves are produced by the carbon particles and the interior surface of the furnace. So, the radiation from flame space to glass liquid can be increased by increasing the blackness of flame and masonry. The blackness of flame can be increased by using hypoxia media or increasing carbon. The blackness of masonry can be related to the roughness and temperature of the surface. The blackness of fireclay bricks and silica bricks at high temperature is respectively 0.61-0.62 at 1000℃, 0.52-0.53 at 1200℃ and 0.47-0.49 at 1400℃. The blackness of fused cast refractories is 0.4-0.5 at high temperature.
(2) The second way is to enforce homogenizing. After the batch materials are loaded into the furnace, the uniformity of mixture is difficult to maintain, which causes nonuniform composition distribution. The heat permeability of molten glass and the heat radiation to the surroundings cause the unevenness of temperature. Homogenizing through natural diffusion is not enough. For this reason, measures should be taken to enforce homogenizing.
Currently measures that have been proven effective include bubbling at the bottom and stirring, discharge and electric heating in the feeding channel. When using the stirring method, pay attention to the stirring position, the insertion depth of the stirrer and the stirring process. The discharge can be continuous or discontinuous. The electric heating can improve the temperature uniformity in the depth direction of the feeding channel, but it may not work for the temperature distribution in the horizontal direction. When taking enforcing measures, make full use of the natural diffusion at the same time.
(3) Reducing unwanted heat loss and repeated heating can also reduce energy consumption. Unwanted heat loss includes the heat dissipation from the furnace surface, heat radiation from the holes and heat taken away by gases through holes and joints. These heat loss can be reduced by insulating and sealing of holes and joints. Repeated heating mainly refers to the reheating of reflux glass liquid. Those heat can be reduced by setting dam walls, sinking the throat, reducing the height of throat and reducing the temperature of glass liquid flowing into the throat.
(4) Refining in the shallow layer, reclaiming in the deep layer and reducing reflux can also reduce energy consumption. The measurement can be taken is setting dwarf wide dam walls.
(5) Another way is to build a stable feeding system. The stability of the shape, size and temperature of gobs is a prerequisite to ensure the quality and yield of the glass molding. The partition between the feeding channel and the work tank, the cross-section, size, insulation, the heating and cooling system of the feeding channel affect the stability of feeding.
(6) Changing the formulation and spheroidizing the batch materials can also reduce energy consumption. Mixing a small amount of flux components such as lepidolite into the raw materials can reduce the melting temperature of glass and accelerate the melting of glass. Spheroidizing the batch materials can eliminate the dust inside and outside the furnace, accelerate the solid phase reaction and increase the contact area between the batch materials and glass liquid. as a result, the melting time is reduced, the service life is expanded and the energy consumption is reduced.
(7) Improving the utilization of heat is an effective energy-saving way. First, ensure the full combustion of fuels to release all the heat. When fueled with heavy oil, select nozzles with good atomization. When fueled with coal gas, determine the reasonable air to coal gas ratio. Then, improve the heat transfer efficiency and maximize air preheating temperature. Therefore, we must increase the heated surface area of checker bricks and the highness of checker bricks. New checker bricks and their arrangement can be adopted. Finally, reuse the heat in exhaust gases.
(8) High quality refractory materials and reasonable combination can also reduce the energy consumption. Currently, the use of high quality refractory materials (such as fused cast refractories, chrome refractories, zircon refractories, corundum refractories, spinel refractories and basic refractories) and their reasonable combination improve the service life of the furnace. the quality of refractory materials also affects the production capacity, the glass quality, the energy consumption and service life of the furnace.
Zhengzhou Sunrise Refractory Co., Ltd. is a refractory supplier from China, specializing in refractory materials for glass furnaces. Our main products are as follows: fused cast AZS 33#,36#,41#, glass furnace fireclay bottom block, mullite brick, zircon brick, alumina bubble brick, sillimanite brick, corundum brick, low porosity fireclay brick, high alumina brick, all kinds of glass furnace ramming masses, sealing materials, building fireclay, etc.
Send an Inquiry
E-mail : sales@sunriserefr.com
Phone : +86-371-63838939 / Fax:+86-371-63835539
Company Address : No.36 Fengchan Road Of Zhengzhou, Henan, China (Mainland)
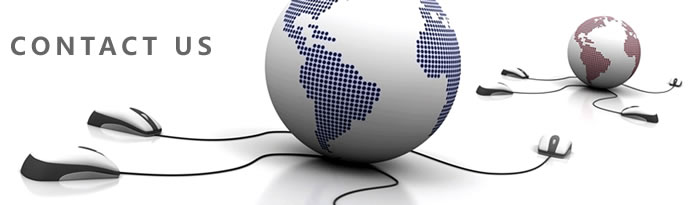
If you have any needs our help or are interested in our products, you can click online advisorychat with us online, or call our customer service telephone: 0086-0371-63838939. We will sincerely serve for you!
Product Category
- Fused Cast AZS
- Fused Cast AZS Block
- Fused Cast Skid Rail Block
- Fused Cast High Zirconia Block
- Fused Cast AZS Block
- Fiber Products
- Insulation Series Brick
- Fireclay Brick
- High Alumina Brick
- Corundum Brick
- Sillimanite Brick
- Mullite Brick
- Zircon Mullite Brick
- Zircon Brick
- Magnesia Brick
- Silica Brick
- Fused Cast Alumina Block
- Glass Mould Brick
Refractory Knowledge
moreCase
UAE to our factory inspection bri
...
Venezuela customer AZS fused bric
Venezuela customer AZS fused float glass furnace br...