Factors of refractory alteration in glass pool kiln
Date:2018-07-24 10:00 From:Zhengzhou Sunrise Refractory Author:sunrise
During the glass melting process, the refractory material and the glass liquid interact at high temperatures, causing the refractory material to be damaged by erosion and even causing defects in the molten glass. The erosion of the refractory by the batch components in the kiln is much greater than that of the glass. Glauber's salt mixture is stronger than alkaline compounding. Usually the erosion of molten soda is limited to the vicinity of the feed port, and thenardite can almost erode to the entire wall. It contains a compound such as boric acid, phosphoric acid, fluorine, chlorine, lead, bismuth and a compound with a high alkali content, and its glass liquid has a particularly strong erosive effect on the refractory material. The structure of the kiln, the chest wall, the small furnace and the regenerator in the flame space of the pool kiln, although not in direct contact with the glass liquid, is also affected by the different degrees of erosion of the mixed material dust and the liquid surface volatile matter.
The corrosion strength of the glass liquid to the refractory material mainly depends on the physical properties such as the viscosity and surface tension of the glass liquid, and the chemical reaction in the process of being eroded only has a subordinate effect. Molten glass with low viscosity and low surface tension easily wets the refractory material and invades the refractory material along the capillary system of the refractory surface. Glass with more alkali has lower viscosity, and borosilicate glass has less surface tension, and their corrosion to refractory material is also strong.
During the heating process, the batch begins to form a fusible polyacid compound that scatters on the glass surface. These melts then gradually dissolve with the more refractory components, so the refractory material in the melting zone of the kiln is eroded by the polyalkali silicate. In particular, when the Glauber's salt compound glass is melted, the molten nitrate water floating on the glass surface directly acts on the refractory material. Sodium sulfate melts at 885 ° C and participates in the glass forming reaction until the reaction is complete at about 1440 ° C. Nitrogen, lye and polyalkali silicates are easily absorbed into the pores of the surface of the refractory material, causing strong corrosion of the refractory material.
When the refractory of the kiln is subjected to physical and chemical attack, the erosion rate is a function of temperature. The erosion rate increases in logarithmic relationship with increasing temperature.
Increasing the melting temperature reduces the viscosity of the molten glass, which accelerates the erosion of the refractory material, thereby greatly shortening the service life of the refractory material. Each elevated melting temperature of 50 to 60 ° C in the kiln will shorten the life of the refractory material by about 1/2. In the kiln, as long as the melting temperature is increased by 20 to 40 ° C, the service life of the crucible is shortened by 1/2.
The resistance to physical and chemical attack of refractory materials is mainly determined by the type of its constituent phases and their distribution and bonding state. Generally, the refractory material consists of one or more crystal phases, a glass phase, and a gas phase (pores). The glass phase is less chemically stable than the crystal, which is the passage of the etchant into the interior of the refractory material (especially the open pores). The depth of penetration of the components of the glass or batch into the refractory pores is proportional to the fourth power of the pore diameter. The etchants first act on the glass phase in the refractory material and react with each other. After the solution infiltrates into the refractory and dissolves the glass phase, the crystals in the refractory are eroded by the flow of the glass and there is a potential for new parts that continue to be eroded. Most of the pores and the glass phase are present in the sinter of the sintered refractory material, so the conjugate becomes a weak point for the refractory material against physical and chemical attack.
The greater the viscosity of the molten material formed by the erosion of the refractory material, the denser the material, and the less open pores, the less the degree of erosion will be. Since the refractory material is dissolved to increase the viscosity of the glass liquid, a protective film which is rarely moved on the surface of the refractory material can be formed, thereby weakening the erosion.
In order to obtain a refractory material with good corrosion resistance, in addition to a stable crystal phase, high softening temperature, high melt viscosity, low glass phase and low porosity, the crystal phase of the crystal phase is required to be fine and uniformly distributed in the glass. In the phase, the structure is uniform and the bonding is tight, so that the glass phase can be enhanced.
The surface of the refractory material is uneven, and cracks and cracks will deepen the erosion, especially the horizontal joint is more seriously eroded. The denser the masonry, the finer the gap, the less the erosion of the glass on the brick wall.
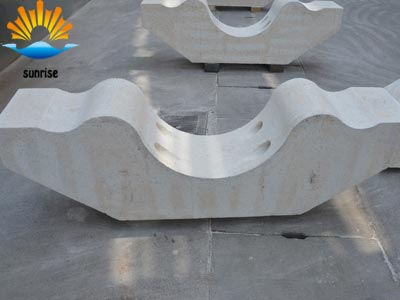
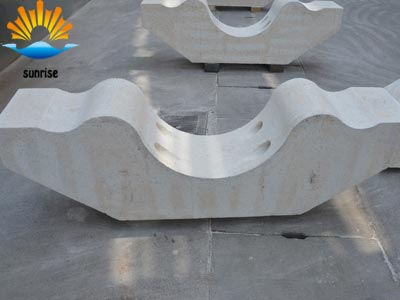
Send an Inquiry
E-mail : sales@sunriserefr.com
Phone : +86-371-63838939 / Fax:+86-371-63835539
Company Address : No.36 Fengchan Road Of Zhengzhou, Henan, China (Mainland)
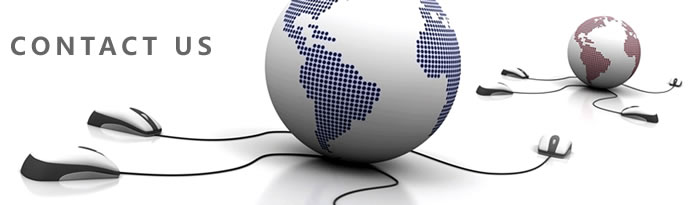
If you have any needs our help or are interested in our products, you can click online advisorychat with us online, or call our customer service telephone: 0086-0371-63838939. We will sincerely serve for you!
Product Category
- Fused Cast AZS
- Fused Cast AZS Block
- Fused Cast Skid Rail Block
- Fused Cast High Zirconia Block
- Fused Cast AZS Block
- Fiber Products
- Insulation Series Brick
- Fireclay Brick
- High Alumina Brick
- Corundum Brick
- Sillimanite Brick
- Mullite Brick
- Zircon Mullite Brick
- Zircon Brick
- Magnesia Brick
- Silica Brick
- Fused Cast Alumina Block
- Glass Mould Brick
Refractory Knowledge
moreCase
UAE to our factory inspection bri
...
Venezuela customer AZS fused bric
Venezuela customer AZS fused float glass furnace br...