Refractory properties research
Date:2018-07-11 10:29 From:Zhengzhou Sunrise Refractory Author:sunrise
Thermal properties and electrical conductivity of refractory materials
1.1 Thermal expansion
The GB/T7320 standard has two definitions: the coefficient of linear expansion (relative rate of change of sample length between room temperature and test temperature, expressed in %), and the average coefficient of linear expansion (the temperature of the sample is increased by 1 ° C between room temperature and test temperature). The relative rate of change, in units of 10-6/°C).
GB/T7320 standard measurement principle: the sample is heated to the specified test temperature at the specified heating rate, the change of the length of the sample with the increase of temperature is measured, and the linear expansion rate and the specified temperature of the sample with the increase of temperature are calculated. The average linear expansion coefficient of the range and plot the expansion curve.
1.2 Thermal conductivity
The thermal conductivity is defined as the amount of heat transferred per unit area of the material along the direction of heat flow per unit temperature gradient per unit time.
The principle of determining the thermal conductivity is: according to the basic principle of the stable heat conduction process of the Fourier one-dimensional plate, the flow of the heat flow flowing through the central calorimeter after passing through the hot surface of the sample longitudinally to the cold surface in the one-dimensional temperature field per unit time at steady state is determined. The amount of heat absorbed. The heat is proportional to the thermal conductivity of the sample, the temperature difference between the hot and cold surfaces, and the area of the heat absorption surface of the central calorimeter is inversely proportional to the thickness of the sample.
The physical meaning of thermal conductivity refers to the amount of heat passing through a unit of vertical area per unit time under a unit temperature gradient. Thermal conductivity is a physical indicator of the thermal conductivity of a refractory material, and its value is equal to the heat flux density divided by the negative temperature gradient.
1.3 heat capacity
Any substance heats up when heated, but the heat required to heat up 1 °C for different substances of the same quality is different. It is usually expressed by the amount of heat (KJ) required to heat 1 kg of material at normal pressure to raise the temperature by 1 ° C, which is called heat capacity (also called specific heat capacity).
1.4 Conductivity
Refractory materials (other than carbonaceous and graphite products) are poor conductors of electricity at room temperature. As the temperature increases, the electrical resistance decreases and the conductivity increases. The increase is particularly remarkable at temperatures above 1000 ° C, such as heating to a molten state, which exhibits a large electrical conductivity.
2. Mechanical properties of refractories
The mechanical properties of refractory materials refer to the strength, elasticity and plastic properties of materials at different temperatures. The mechanical properties of the refractory are usually judged by indicators such as pressure resistance, flexural resistance, wear resistance and high temperature soft creep.
2.1 Normal temperature mechanical properties
2.1.1 Normal temperature compressive strength
It refers to the maximum pressure that a refractory material is subjected to per unit area at normal temperature. If it exceeds this value, the material is destroyed. If A is used to indicate the total area under pressure of the sample, and P is the limit pressure required to crush the sample, then: normal temperature compressive strength = P / A (Pa)
Generally, refractory materials rarely cause damage due to static load at normal temperature during use. However, the normal temperature compressive strength mainly indicates the sintering condition of the product, and the properties related to its structure, and the measuring method is simple, so it is a common inspection item for judging the quality of the product.
2.1.2 Tensile, flexural and torsional strength
When used, in addition to compressive stress, refractory materials are also affected by tensile stress, bending stress and shear stress. The main factors affecting the tensile and flexural strength of refractory products are their microstructure. Fine particle structure is beneficial to these indicators. Improvement.
2.1.3 wear resistance
The wear resistance of a refractory material depends not only on the density and strength of the article, but also on the mineral composition of the article, the firmness of the structure and the combination of material particles. The normal temperature resistance is high, the porosity is low, the structure is dense and uniform, and the sintered product always has good wear resistance.
2.2 High temperature mechanical properties
2.2.1 High temperature compressive strength
High temperature compressive strength is the ultimate pressure that a material can withstand at a high temperature. As the temperature increases, the strength of most refractory products increases, with clay products and high aluminum articles being particularly noticeable, reaching a maximum at 1000-1200 °C. This is because the viscosity of the melt formed at a high temperature is higher than the viscosity of the fragile glass phase at a low temperature. But the bond between the particles is stronger. As the temperature continues to rise, the intensity drops dramatically. The high temperature compressive strength index of the refractory material can reflect the change of the bonding state of the product at high temperature.
2.2.2 high temperature flexural strength
High temperature flexural strength refers to the ultimate bending stress that a material can withstand at a high temperature. It characterizes the ability of materials to withstand bending moments at elevated temperatures.
The high temperature bending strength is also called high temperature bending strength or high temperature breaking modulus. The maximum load that can be withstood when a rectangular test piece of a certain size at a high temperature is bent on a three-point bending device is measured.
The high temperature strength of refractories is closely related to their actual use. Especially for evaluating the quality of alkaline directly bonded bricks, high temperature flexural strength is an important property. If the high-temperature bending strength of the alkaline direct bonding brick is large, the shear stress generated by the temperature gradient is strong, so that the product is not easily peeled off during use. Products with high high-temperature flexural strength will also improve the impact and wear of the materials and enhance the slag resistance. Therefore, the high-temperature flexural strength is used as an indicator to characterize the strength of the product.
The high temperature flexural strength index of refractory materials mainly depends on the chemical mineral composition, structure and production process of the products.
2.2.3 High temperature creep
When the material is subjected to a constant load at a high temperature that is less than its limit, plastic deformation occurs, and the amount of deformation gradually increases with time, and even the material is destroyed. This phenomenon is called creep. Therefore, for materials at high temperatures, the strength cannot be considered in isolation, and both temperature and time factors and strength should be considered. For example, the damage of the hot blast stove bricks working at high temperatures for a long time is due to the softening of the brick body to produce plastic deformation, and the strength is significantly reduced or even destroyed. This creep phenomenon of the lattice bricks is the main cause of furnace damage.
The factors that affect high temperature creep are generally considered to be: 1) conditions of use such as temperature and load, time, atmosphere properties, etc.; 2) materials such as chemical composition and minerals; 3) microstructure. The high temperature creep curve of the material is divided into three stages, the first stage creep becomes deceleration creep (time is short); the second stage is uniform creep (minimum creep rate); the third stage is accelerated creep (creep rate) Rapid increase).
3. High temperature use properties of refractory materials
3.1 Refractoriness
The property that the refractoriness resists high temperature when it is not loaded and does not melt is called refractoriness. For refractory materials, the meaning of refractoriness is different from the melting point. The melting point is the temperature at which the crystalline phase of the pure substance is in equilibrium with its liquid phase. However, the general refractory material is a heterogeneous solid mixture composed of various minerals, not a pure phase of a single phase, so there is no melting point, and the melting is carried out within a certain temperature range, that is, only a fixed initial melting temperature and A fixed melting end temperature. In this temperature range, the liquid phase and the solid are present at the same time.
The refractoriness is a technical index. The measuring method is a truncated triangular cone made of test materials. The upper side is 2 mm long on each side, and the lower bottom is 8 mm long and 30 mm high. (The angle between the side and the vertical direction is 80) Equilateral triangle. When heated at a certain heating rate, it gradually deforms and bends due to its own weight. When it is bent until the apex is in contact with the chassis, it is the refractoriness of the sample.
3.2 high temperature volume stability
When the refractory material is used for a long period of time at a high temperature, the performance of the outer shape of the refractory material which remains stable without undergoing a change (shrinkage or expansion) is called high temperature volume temperature. It is an important indicator for assessing the quality of a product.
During the firing process, the physicochemical changes in the refractory material generally do not reach the equilibrium state at the firing temperature. When the product is subjected to high temperature for a long time, some physical and chemical changes will continue. On the other hand, in the actual firing process, for various reasons, there may be insufficiently baked products. When such products are used in a kiln and then subjected to high temperature, some firing changes continue, resulting in products. The volume changes—contraction or expansion—this irreversible volume change is called residual shrinkage or expansion, also known as reburning shrinkage or expansion. The size of the reburning volume change indicates the high temperature volume stability of the product.
3.3 Thermal shock stability
The property of a refractory material against a sharp change in temperature without damage is called thermal shock stability. It is well known that materials rise or contract with temperature rise and fall, and if this expansion or contraction is constrained and cannot develop freely, stress is generated inside the material. Such internal stress caused by thermal expansion or contraction of the material is called thermal stress. Thermal stress is generated not only under mechanical constraints, but also in temperature gradients in the homogeneous material, the difference in thermal expansion coefficients between the phases in the heterogeneous solid, and even the anisotropy of the thermal expansion coefficient in the single-phase polycrystal. Both are the source of thermal stress.
Thermal shock damage of refractory materials can be divided into two categories: one is instantaneous fracture, called thermal shock fracture; the other is cracking, spalling, then fragmentation and deterioration under the action of thermal shock cycle, and finally The overall damage is called thermal shock damage.
four. Refractory development prospects
In the future, the main direction of refractory technology development should be based on the characteristics of China's raw material resources, comprehensively improve quality, develop high-quality and efficient new products at the end point, adopt advanced technology, technological innovation and upgrade equipment to improve the use effect, reduce the consumption of use, and adapt to the high temperature technology. Claim. The specific future development prospects are as follows:
1. High quality raw materials This is the basis for the development of high quality refractory materials. A lot of research should be done in mineral processing, purification, synthesis technology, exercise technology and so on. The purity of raw materials is improved, the degree of sintering is improved, the composition of the components is uniform, and the performance is stable, which provides a basis for the development of high-quality, high-purity and high-efficiency products. The proportion of natural refractory raw materials is gradually increasing, and the proportion of high-purity, high-density and uniform-quality refractory raw materials after beneficiation and synthesis is continuously increasing. In addition, in the development of new varieties of refractory materials, we should also research and develop high-quality, high-efficiency, high-aluminum and alkaline products based on China's resources and needs.
2. The transformation to quality is characterized by energy saving, labor saving, multi-variety, high quality, low output and high profit. It accelerates the transformation of refractory materials from quantity to quality and from labor-intensive technology-intensive types. change.
3. Develop new varieties including: high temperature refractory products; low energy refractory products; high-tech, high-performance refractory products.
4. The new process requires strict precision, fine matching, high pressure, high temperature, composite technology, and reference to ultrafine powder. By adjusting and controlling the microstructure characteristics, it can improve and optimize high temperature performance, especially the physical properties and thermal shock resistance. And anti-invasive properties. In addition, in order to make the direct bonding and recombination bricks develop to higher purity, higher density and better structure, new processes such as beneficiation and purification, two-step calcination, high-pressure ball formation, artificial synthesis, high-pressure molding and high-temperature sintering are adopted. .
5. Comprehensive consumption of refractory materials It is a comprehensive reflection of all the above technological advances. The continuous reduction in the overall consumption of refractory materials (the ratio of refractory production to steel production) is an important indicator of the development of refractory materials.
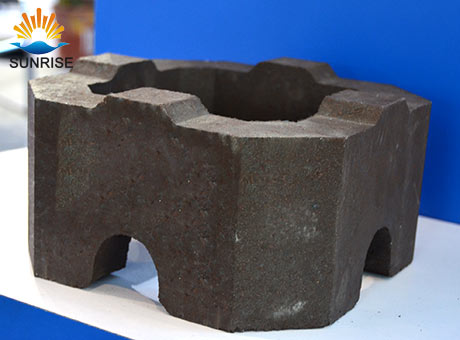
Send an Inquiry
E-mail : sales@sunriserefr.com
Phone : +86-371-63838939 / Fax:+86-371-63835539
Company Address : No.36 Fengchan Road Of Zhengzhou, Henan, China (Mainland)
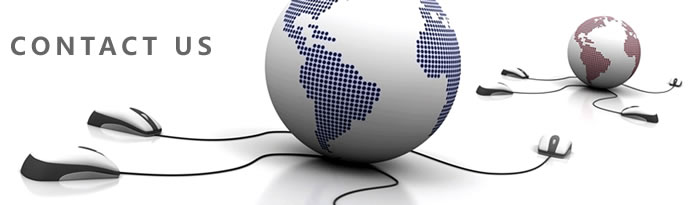
If you have any needs our help or are interested in our products, you can click online advisorychat with us online, or call our customer service telephone: 0086-0371-63838939. We will sincerely serve for you!
Product Category
- Fused Cast AZS
- Fused Cast AZS Block
- Fused Cast Skid Rail Block
- Fused Cast High Zirconia Block
- Fused Cast AZS Block
- Fiber Products
- Insulation Series Brick
- Fireclay Brick
- High Alumina Brick
- Corundum Brick
- Sillimanite Brick
- Mullite Brick
- Zircon Mullite Brick
- Zircon Brick
- Magnesia Brick
- Silica Brick
- Fused Cast Alumina Block
- Glass Mould Brick
Refractory Knowledge
moreCase
UAE to our factory inspection bri
...
Venezuela customer AZS fused bric
Venezuela customer AZS fused float glass furnace br...