Lightweight silicon brick production process
Date:2018-06-04 10:20 From:Zhengzhou Sunrise Refractory Author:sunrise
Lightweight silica bricks, also known as silica insulation bricks. More than 91% of silica, with a bulk density of 1.2g/cm3 or less, is a lightweight refractory material. The refractoriness and load softening temperature are similar to ordinary silica bricks with the same composition. Using finely divided silica as a raw material, its critical particle size usually does not exceed 1 mm, and particles smaller than 0.5 mm therein are not less than 90%. The flammable substances are added to the ingredients or a porous structure is formed by a gas generation method and is obtained by firing.
Production of lightweight silica bricks:
(1) Raw materials, mineralizers and binders
The quartz stone and the waste silicon brick are used as raw materials, broken by a jaw crusher and then crushed into a fine powder with a particle size of <0.088 mm.
Fe2O3 + FeO content> 95% of the scale and CaO content> 20% of the digested lime as a mineralizer; with a concentration of Baume 14 degrees calcium lignin solution as a binding agent.
(2) Preparation of mud
The formulation of mud is: quartz powder 65%, waste silicon brick powder 35%, lime milk added 14%, iron scale 1.5%, bone glue 0.5%, calcium lignosulfonate 3%, water 45-48%.
The above-mentioned well-matched material is put into a pebble ball mill for more than 10 hours and passed through a 0.048 mm sieve, which is a slurry.
(3) Preparation of foaming agent
It is formulated with sodium rosin foaming agent and stabilizer, bone glue solution.
Sodium rosin acid foaming agent is rosin and alkali saponification, the ratio is: rosin: sodium hydroxide: water = 10:1:10, the three will be heated to melt the foaming agent.
Stabilizer - the proportion of bone glue solution: bone glue: water = 16:72.
The formulated sodium rosin foaming agent is added to the stabilizer, a bone glue solution, and the mixture is stirred and foamed.
When foaming agent is used, dilute it with 8 times hot water and put it in a foaming tube for 15 minutes.
(4) Preparation of foam mud
Put the well-watered slurry into the beater, add 0.1-0.15% of the weight of the alum to the slurry, stir for 2 minutes, and then add the foaming agent, which is 1% of the weight of the slurry, and stir until the surface is free of foam. The bulk density of the foamed mud is 0.65 g/cm3. The prepared foam slurry must not be released for a long time to prevent its quality from being affected.
(5) Casting and drying
On a perforated aluminum slat (or floor), a bottomless wooden mold of size 285 x 150 x 100 mm is placed, waste paper is placed between the aluminum slat (or ground) and the wood mold, and the foamed mud is poured into the wooden mold. And to make its surface convex, in order to avoid the depression of the refractory brick brick after drying.
The bricks were dried in a tunnel drier and dried at a temperature of 30-45°C. After drying for 24 hours, they were released from the mold. After 48 hours, they were turned sideways. The water content of the 96 hours light refractory brick bricks was <3%, which could be calcined.
(6) Firing and Finishing
The bricks are fired together with the silica bricks in the tunnel kiln. The kiln is mounted in frame and the bricks can be placed vertically. The firing system is the same as that of ordinary silicon bricks. The firing temperature is 1350-1375°C. Insulation 32h, the total firing time of 196h, the yield was 92.80%.
The fired bricks (or blanks) are cut and ground by a grinder and processed into various types of products.
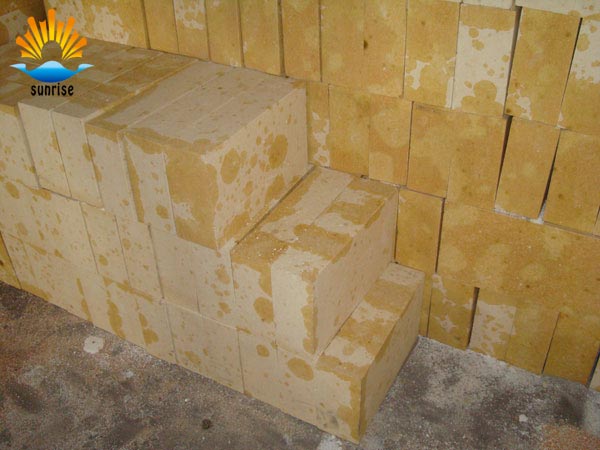
Send an Inquiry
E-mail : sales@sunriserefr.com
Phone : +86-371-63838939 / Fax:+86-371-63835539
Company Address : No.36 Fengchan Road Of Zhengzhou, Henan, China (Mainland)
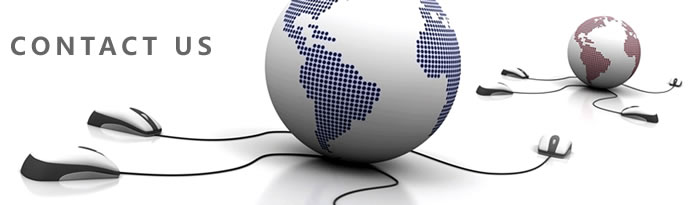
If you have any needs our help or are interested in our products, you can click online advisorychat with us online, or call our customer service telephone: 0086-0371-63838939. We will sincerely serve for you!
Product Category
- Fused Cast AZS
- Fused Cast AZS Block
- Fused Cast Skid Rail Block
- Fused Cast High Zirconia Block
- Fused Cast AZS Block
- Fiber Products
- Insulation Series Brick
- Fireclay Brick
- High Alumina Brick
- Corundum Brick
- Sillimanite Brick
- Mullite Brick
- Zircon Mullite Brick
- Zircon Brick
- Magnesia Brick
- Silica Brick
- Fused Cast Alumina Block
- Glass Mould Brick
Refractory Knowledge
moreCase
UAE to our factory inspection bri
...
Venezuela customer AZS fused bric
Venezuela customer AZS fused float glass furnace br...