Cause Analysis of Collapse of Refractory in Circulating Fluidized Bed Boiler
Date:2017-06-09 09:52 From:Zhengzhou Sunrise Refractory Author:sunrise
Circulating fluidized bed boiler in the selection of refractory materials, construction and operation and maintenance, there are still many problems to be resolved, in which refractory often collapse of the current troubled circulating fluidized bed boiler long-term safe, stable, continuous operation of the main reasons The
Refractory material with the temperature rise and fall, resulting in expansion or contraction, if the expansion or contraction is bound, the material will produce internal stress. Refractory material is heterogeneous brittle material, compared with metal products, because of its thermal conductivity and elasticity, low tensile strength, resistance to thermal stress damage is poor, low thermal shock resistance, in the thermal shock cycle , Refractory material first cracked to the overall damage, which is circulating fluidized bed boiler refractory early failure of the important reasons. Factors that affect the thermal shock stability of refractories are complex and need to take into account the effects of various factors.
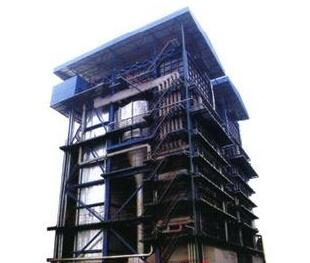
Circulating fluidized bed boiler
The physical and chemical properties of refractories are very important. High temperature pressure strength indicators should also be considered. Some castables in the circulating fluidized bed boiler combustion temperature can not be used to achieve the sintering temperature and low strength, such as adding high-alumina cement castable, due to the increase in calcium content, room temperature and 100 ℃ after drying strength Peak, but with the increase in temperature strength decreased at 700-1000 ℃ when the lowest strength. There are many kinds of refractory binder to be more than 1200 ℃ temperature sintering after a certain strength, the use of 1200 ℃ below, because the refractory material does not reach the sintering temperature and lead to low strength, therefore, in the circulating fluidized bed boiler Selection effect is not ideal.
Construction, installation and oven unreasonable refractory material is one of the main reasons. Most manufacturers have no construction and installation experience, in the construction and installation can not be strictly in accordance with the design requirements, the material production plant to provide the construction requirements of refractory construction supervision. Some installation companies do not have experience in the installation of circulating fluidized bed refractories, according to the industrial boiler masonry methods and experience in the construction, resulting in a larger installation quality defects. There are individual projects in order to shorten the installation period ahead of schedule, because the oven did not meet the requirements, so that the moisture contained in the material is not fully converted to water vapor escape, the boiler ignition after the fire when the water vapor pressure exceeds the material Tensile strength, causing the lining layer and collapse, resulting in furnace ignition soon caused the furnace wall, the return of the device, the ignition duct and slag cooler, etc. a large area of collapse.
The main reason for the destruction of refractory material is the temperature cycle fluctuations and thermal shock and mechanical gravity caused by refractory cracks and peeling, and the impact of solid material damage. This effect can not be avoided, so take appropriate measures to improve the tolerance of refractories. To prevent the collapse of refractory material is mainly concerned with the structural design of refractory materials, construction and operation and maintenance. Material must be high strength refractory, wear resistant material, with good bending strength. Refractory, wear-resistant coating on the refractory level should be designed metal pins, the length of the basic through the refractory layer thickness, or in refractory, wear-resistant materials, stainless steel fiber, uneven expansion in the cracks, not a large area off. Fire-resistant, wear-resistant materials, maintenance is also very important, if the use of wood oven, the general dense area of the refractory layer can be better curing; oven, the refractory surface to reach and exceed the sintering temperature is critical.
I unit is a boiler for the Wuxi Huaguang Boiler Co., Ltd. manufacturing model: ug-75 / 5.3-m19, in July 2007 began to install, September 28 after the end of the hydraulic test, they entered the building Construction, wear-resistant refractories are mainly arranged in the furnace area, the water-cooled room part, the furnace outlet part, cyclone separator (including import and export flue), the feeder and other parts. On November 16, the boiler masonry work was completed and the oven was prepared.
For the boiler wear-resistant refractory design, the oven is divided into four steps, namely: water-cooled room and ignition, furnace density zone, return valve, cyclone separator cone.
Implementation of the specific process: After the expiration of the natural conservation of refractory materials, in the water-cooled wind chamber into the firewood, baking it alone for 48 hours, while the return valve baking, cross to save the oven time, but must be in the material Valve at the bottom of the hood bedding bed, the thickness of more than 100 mm away from the hood. To ensure that the hood is not burned. After the end of the baking stage of the water-cooled wind chamber, the temperature of the dense phase of the furnace can enter the work, the bed material is laid on the cloth board, and the thickness is about 100 mm above the hood, and then the second step can be carried out. Back to the valve uninterrupted baking. Furnace dense area baking, due to the hot and cold air convection in the furnace to form a negative pressure caused by the bake can not be fed back into the material, the return valve to stop the baking and other furnace area after baking finished, and then the third Step, in the return valve within the wood baking 2 days. Back to the valve bake two days later, in the cyclone separation cone made of steel frame on the firewood into the fourth step baking process, the specific heating rate see the heating rate curve.
The baking time of each part: water-cooled room and igniter bake 2 days, the furnace dense area bake 7 days, back to the valve bake 2 days, whirlwind separator cone baking at least 7 days, in order to save baking Furnace time, during which the furnace baking site time can be interspersed at the same time baking, depending on the actual situation may be.
As the duration of tension, in the boiler masonry work the end of the second day, they enter the low, medium temperature oven, sacrificed the natural conservation period of refractories.
The baking of the cone part of the cyclone separator, due to the shortage of wood, with the duration of tension, only baked for two days. With the high temperature oven stage of the boiler, due to the lack of understanding of the importance of refractories, management negligence, resulting in 3 days 2 times the boiler water, resulting in the loss of liquid, the last oven had to end.
In the initial start of the boiler, the operator did not follow the rules to control the heating rate, from the ignition to the normal working pressure (5.3mpa) took only 2 hours, the results of the boiler at work pressure for 2 hours, Severe coking was forced to stop the furnace, because a large number of castables fall off in the furnace, so that the material flow is not normal, a large number of pouring material pouring material to make the feeder block.
(See Figure 1), the furnace outlet at the furnace wall off (see Figure 3), the fall of the castable thickness of the thickest to reach 60 mm, caught nails have been exposed , And some up to 20 mm, off part of the castable see Figure II.
After the boiler masonry is completed, there is no natural drying period, so that most of the refractory water can not precipitate. In the oven, a large number of water vapor can not be discharged in time to make the fire layer burst and fall off. In the ignition process too fast, due to the resulting water vapor to break through the refractory wear layer, so that the refractory wear layer temperature gradient, resulting in a huge thermal stress, so that the refractory anti-wear layer split and off.
Send an Inquiry
E-mail : sales@sunriserefr.com
Phone : +86-371-63838939 / Fax:+86-371-63835539
Company Address : No.36 Fengchan Road Of Zhengzhou, Henan, China (Mainland)
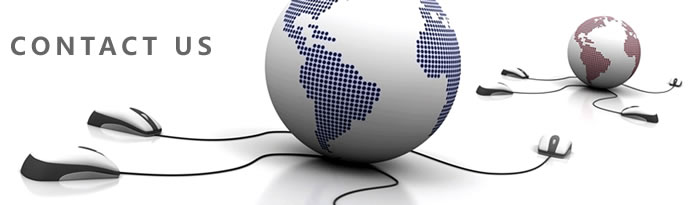
If you have any needs our help or are interested in our products, you can click online advisorychat with us online, or call our customer service telephone: 0086-0371-63838939. We will sincerely serve for you!
Product Category
- Fused Cast AZS
- Fused Cast AZS Block
- Fused Cast Skid Rail Block
- Fused Cast High Zirconia Block
- Fused Cast AZS Block
- Fiber Products
- Insulation Series Brick
- Fireclay Brick
- High Alumina Brick
- Corundum Brick
- Sillimanite Brick
- Mullite Brick
- Zircon Mullite Brick
- Zircon Brick
- Magnesia Brick
- Silica Brick
- Fused Cast Alumina Block
- Glass Mould Brick
Refractory Knowledge
moreCase
UAE to our factory inspection bri
...
Venezuela customer AZS fused bric
Venezuela customer AZS fused float glass furnace br...